【 CB125 ステップ周り製作
】 (Nov/2012)
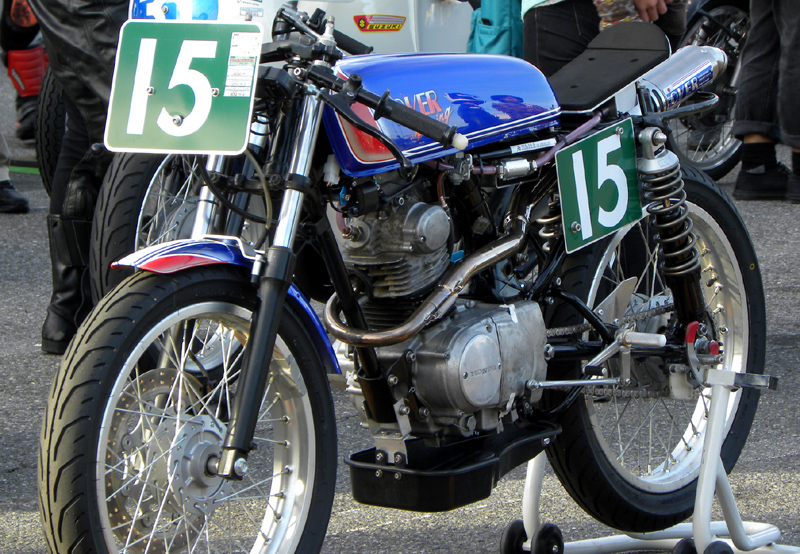
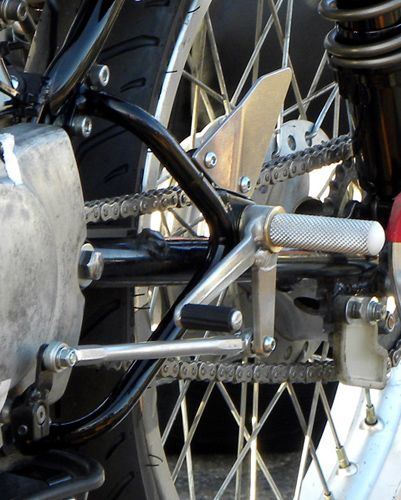
|
|
【 サイレンサー製作
】 (Nov/2012)
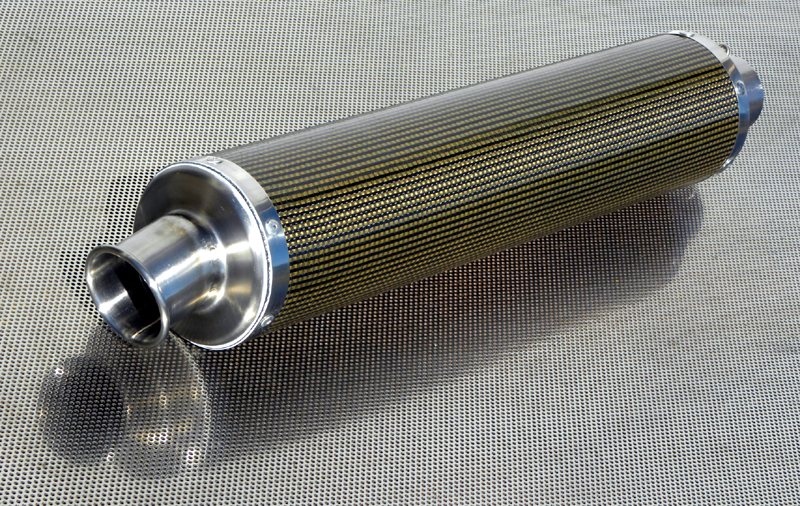
昨年マフラーを作った
VFR750のお客さんに、軽量なレース用サイレンサーの製作を依頼された。
今はあまり見なくなった
ケブラーカーボンの外筒、金物は全てチタン板からの単品製作。
|
|
【 ガソリンタンク修理
】 (Oct/2012)
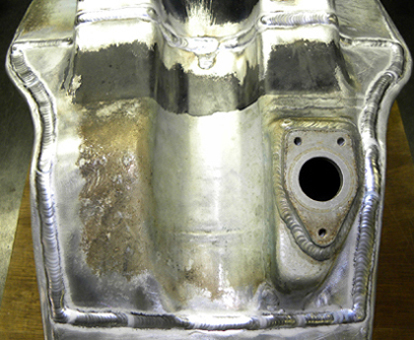
もう古くなってしまったが。TZ250 か 350 のガソリンタンクだろう。 加減速のGで
ガソリンが前後に大暴れしない様に 仕切り板が入っている。
振動で
3枚の仕切り板の1枚は半壊、もう1枚は完全に脱落して、中でガラガラ遊んでいた。
作業としては、底板を切開し 仕切り板を再溶接し
蓋をするだけの単純な作業だが、
何せ古いタンクなので、ガソリンは漏れていないが
クラックが入っていたり、擦れて薄くなっていたり、気にし出したら切りが無いが
せっかくなので 補修をし、最後に エアーで加圧して
漏れ検査をして終了。 結構 時間も掛かるし、気も使う作業だ。
|
|
【 キャリパーピストン製作
】 (May/2012)
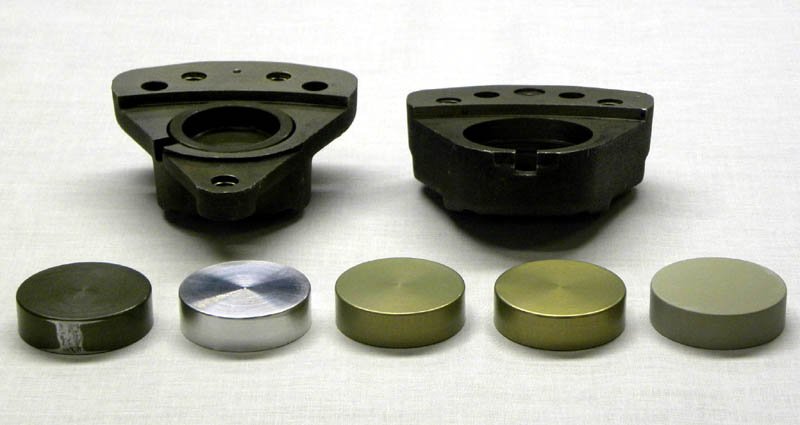
古いレーサーのブレーキ キャリパーピストンの製作。 左端のものがオリジナルで
表面のアルマイトが剥がれて地肌が出てしまっている。
もう部品を入手出来ないので、1個だけだが加工し
ハードアルマイト処理をした。 何故こんなに沢山あるのか?・・・失敗しまくったのだ・・・
左から、オリジナル、機械加工品、ハードアルマイト処理後、研磨仕上げ後、そしてアルマイト処理を失敗して溶けてしまった物。
ピストンの形状は単純だが、ブレーキパッドの温度は300°を超えるので、熱膨張の大きいアルミピストンの場合、シリンダーとのクリアランスは
かなり大きめにする必要がある。 更にピストンの倒れによる
かじり対策の為、面取り形状には
それなりのノウハウが必要だ。
アルマイトの膜圧と、研磨で、最終的にクリアランスをコントロールする訳だが・・・
いずれにせよ、ブレーキは重要保安部品なので、素人が加工してはいけません、極めて危険です。 今回は走行会で楽しむ程度と言う事で・・・
たった
これ1個作るのに、とっても多くの知識を得た・・・のだが、大赤字・・・トホホ
|
|
【 撮影用機材
】 (Apr〜Jun/2012)
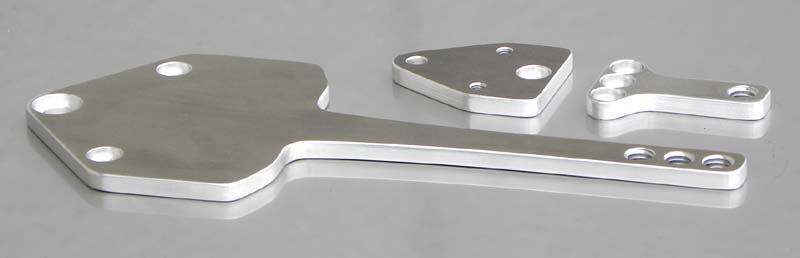
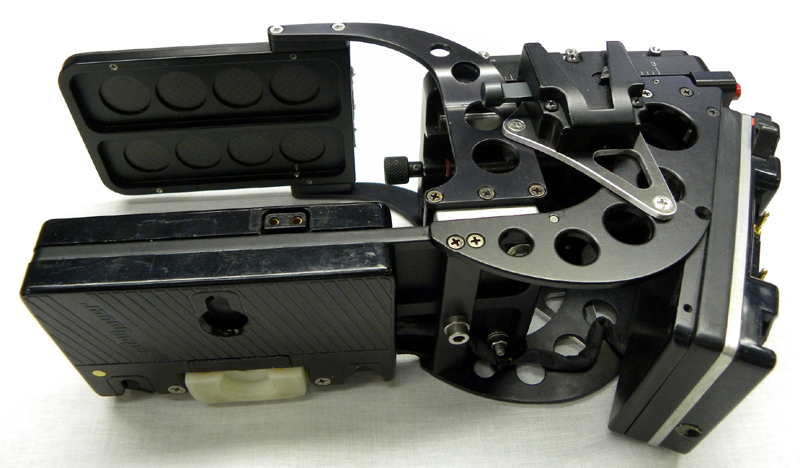
様々なバッテリーホルダー等を取り付ける為、増築増築を繰り返し
迷路になっている古い温泉宿の様に、ステーをどんどん追加製作していくうちに
何が何だか分らなくなって来た
撮影器具。 そろそろスッキリと作り直したいところだが・・・
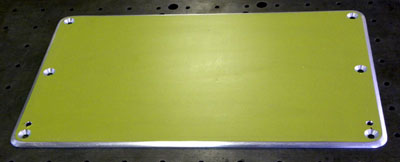 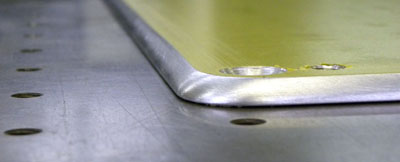
ただのアルミの板を切って 穴あけ、ネジ切り、しただけ。 これから
この板に沢山ネジ切りをして、色々な機材を取り付けるのだが、
床に据付けるので、段差があると
つまずいてしまう為、周りを斜めに削って 角を落としてある
又、厚くない板なので、ネジ穴には全て
ヘリサートコイルを挿入する
ちなみに、こんな風に熔接加工等せず、ある程度の強度が必要な場合は、 JIS規格の A2017
というアルミ合金を使う事が多い
A2017 は、純アルミに比べ 遥かに高強度だが、耐食性、熔接性が劣る。 通常
ジュラルミン と呼ばれているのが、A2017 である
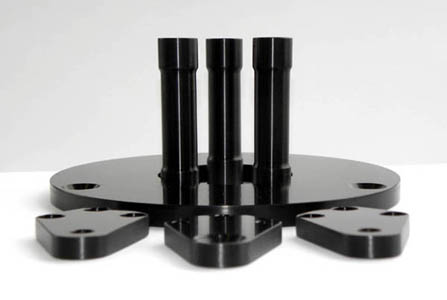
昨年作った 3本足の自在テーブルの仕様違い、柱を立てて上に円板を取り付け、その上に又
機材を取り付けていく。 黒アルマイト処理。
アルミニウムは、素材のままでも
表面に薄い酸化皮膜を生成するので、耐食性はあるが
柔らかく傷つきやすい為、耐摩耗性向上と
より耐食性向上を目的にした、陽極で電解し酸化させ 陽極酸化皮膜を作る処理をする。 それが
Alumite 処理である
今回は この酸化皮膜処理後、染料に浸して黒に着色した。 ちなみに
両端にネジ加工した3本のシャフトは、膜厚を厚くして
より表面を硬質にし、ネジ部の耐久性を上げている
|
|
【 スーパーカート ・
チタンエキパイ改修 】 (Apr/2012)
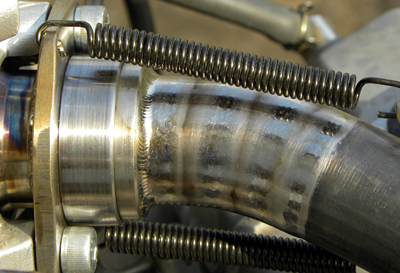
スーパーカート用 YZ250F(WR)
のチタンエキパイ。 シリンダーのエキゾストポートにガスケットを介して がっちりボルトで固定されているので
振動で割れてしまう。 何度か修理したらしいが、何とかならないか?と相談を受けた
そこで、エキパイジョイントを新作し、シリンダーにボルトで固定。 そのジョイントにエキパイフランジを差込み、スプリングで留める事にした
排気ポート出口は
排気圧力が高く、排気漏れしやすいので、本来はエキパイの曲がったRの先のストレート部分に
ジョイントを取り付けるのだが
今回のエキパイは寸法的に不可能で、やむなく 排気ポート出口でジョイントした。 割れたパイプの部分は作り直した
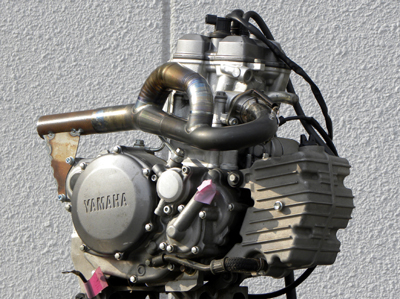
ジョイント部分の排気漏れ対策には、Oリングやウエーブワッシャを使用する方法もあるが、4ストロークエンジンでは
あまり使われていない様だ
いずれにせよ 今回はスペース的に困難で、割れたエキパイのチタンフランジを材料として利用出来る
等の理由から、エキパイジョイントを
ラビリンス構造にして 排気漏れに対応する事にした
|
|
【 Buell サイレンサー
】 (Feb/2012)
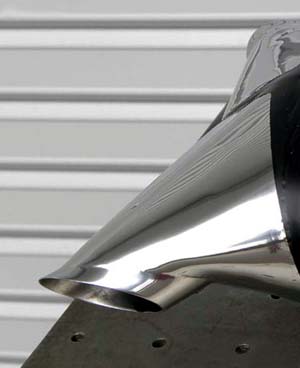
1200ccの車輌だが、900cc用標準マフラーをベースに
内部を作り直し、排気口は左右2本出しに変更。アンダーカウルに隠れ見えるのは排気口のみ
ノーマルのマフラー自体
ただの黒い箱で不細工なのに、排気口が左右2本出てるだけだと更に格好悪いので
出口形状は少し凝ってみた
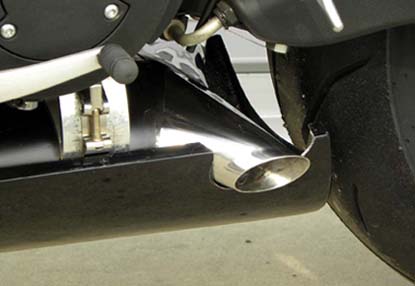
出口内部に付いている部品は、音量を抑える為の小細工
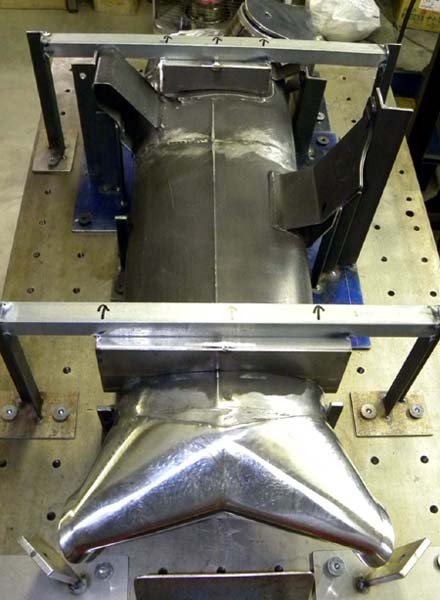
内部構造は完全に作り変えた。 音質、トルク特性、排気効率 etc
能書きは完璧だったはずだが・・音質には殆ど寄与しなかった・・・
おかげで
沢山のノウハウを得られ、すっかり自分の勉強材料にしてしまった
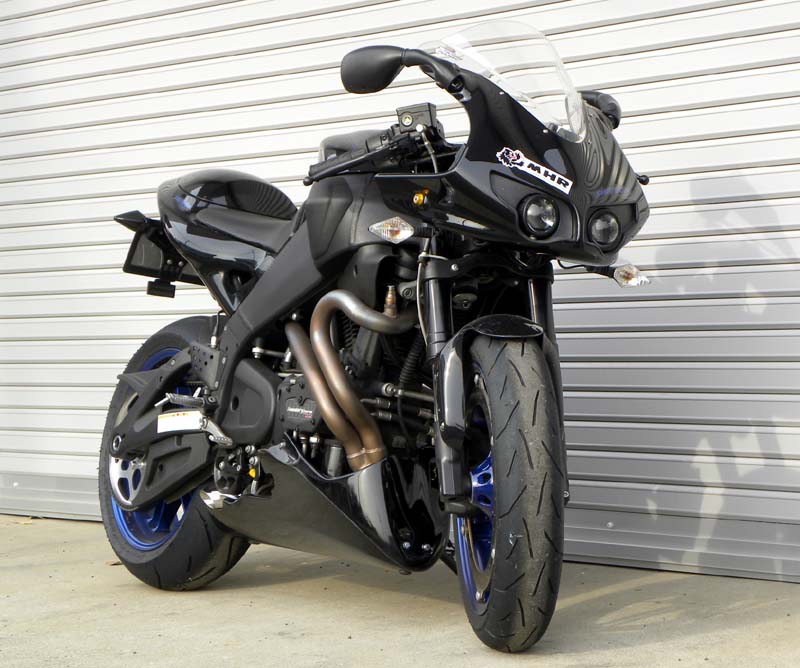
結局、せっかく苦労して作ったマフラーが隠れて、排気口だけが覗いている姿が 最も格好良い。 やっぱり
Buell 様々である
|
|
【 撮影用機材 色々
】 (Dec/2011)
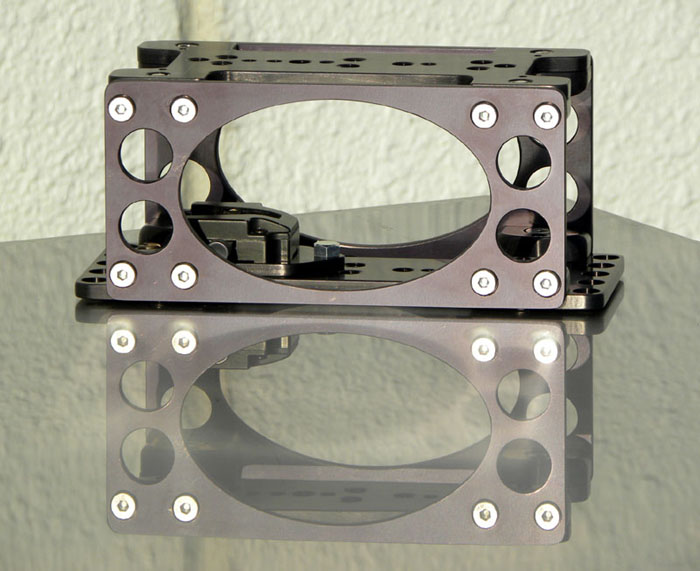
これは何だか分らないと思うが、作ってる本人も よく分らない。 何でも
この下に本格的な撮影用のカメラがぶら下るらしい
何度か リハーサルをして、最終的に この形状や寸法に決まった。 結局
没になった部品が結構あるのだが・・もったいない・・
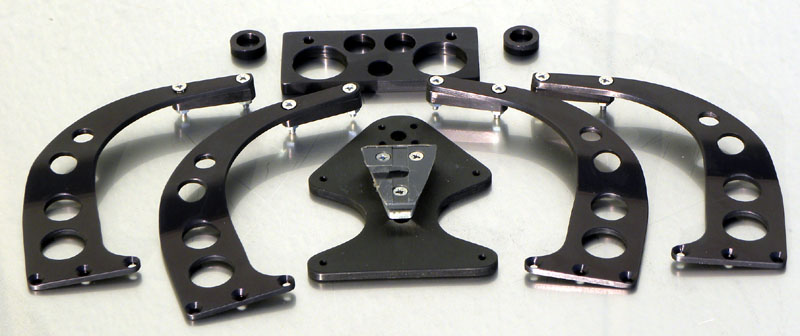
これも同様な機材で、種々のバッテリーやコントロールボックスが取り付き、そこに沢山のコネクターが付いて
コードが出て行く
出来るだけ軽量化したいが、強度も必要だし
スペースが限られている。 全ての物のクリアランスがギリギリだ
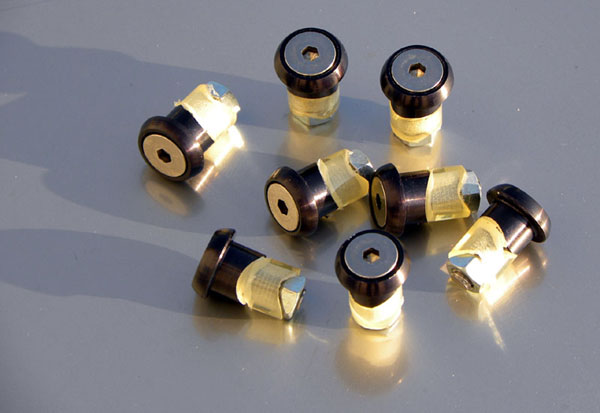
これは 2本並んだパイプの上を部品がスライドする機材で、言ってみれば
フロントフォークの上をトップブリッジがスライドする様なものだが
動かしすぎて
誤って部品がパイプから落ちない様にする為のストッパーだ。 部品は常に交換するので、交換時はすぐに外れなければならない
スプリングでボールが顔を出す方法とか、やはりスプリングでワンウェイの爪が出る方法とか、考えたが
時間的に余裕が無かったのと
コストの問題で、
パイプの中でウレタンゴムが膨らむ方法にした。 しかし決して簡単にはいかなかった
|
|
【 撮影用機材 自在テーブル 】
(Dec/2011)
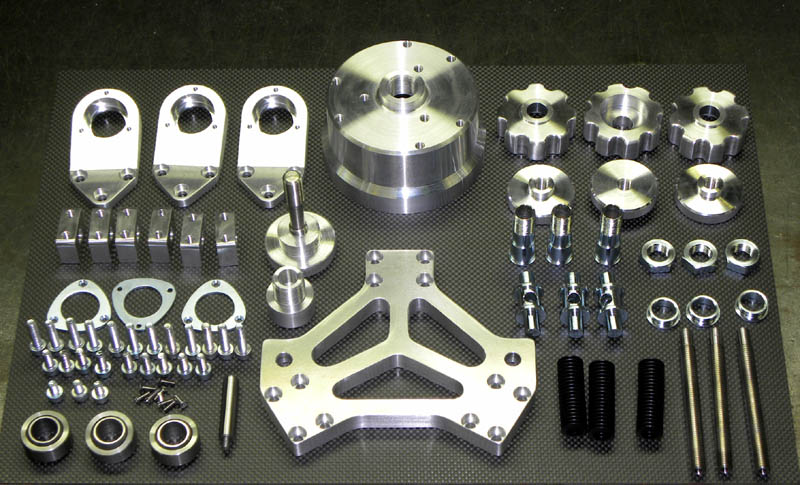
撮影用の機材で、ハンドルを回して
3本の足の長さを変えて
三角形の天板の角度を自在に変更する
天板の上にアタッチメントを取り付け、そこから出るアームの先にカメラが付く
ボルト以外の全てを設計・製作 結構な部品点数になった
出来るだけシンプルに
軽く、更に今後の仕様変更にも対応する様にと、条件は盛り沢山
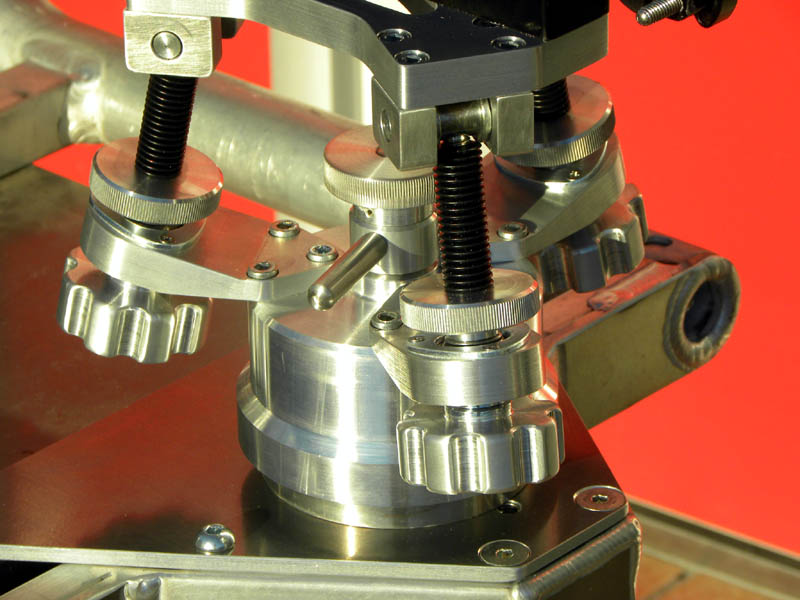
ハンドルの上には スフェリカルベアリングが入っている。 ハンドルで全ネジシャフトを上下させて
上の平目ローレットを切ったハンドルでロックする
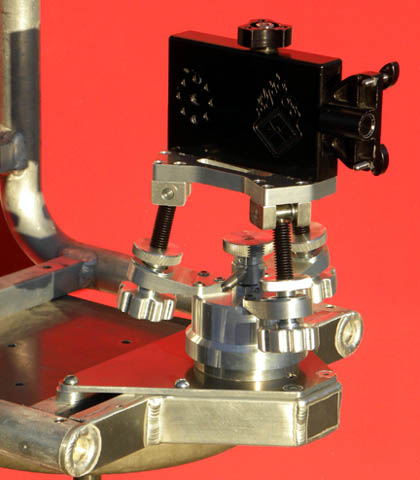 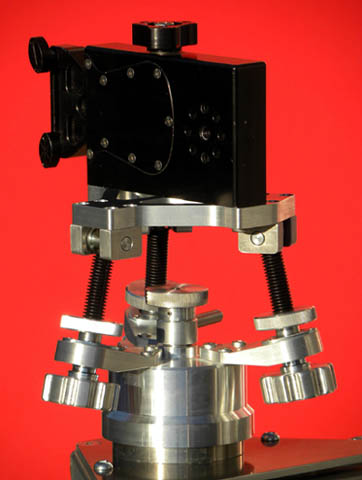
ターンテーブル上の椅子に取り付け、又で挟む格好で使う
撮影用のカメラはデジタル化したので本体は小型になったが
レンズはそのままなので、相当の重量になる
更に、ガタがあると映像が ぶれるので要注意
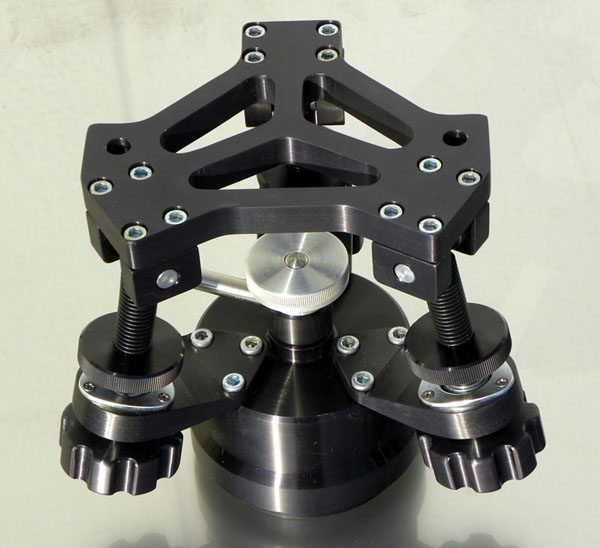
最終的に 黒のハードアルマイト加工をして終了
|
|
【 GB500 チタンエキゾースト 】
(Oct/2011)
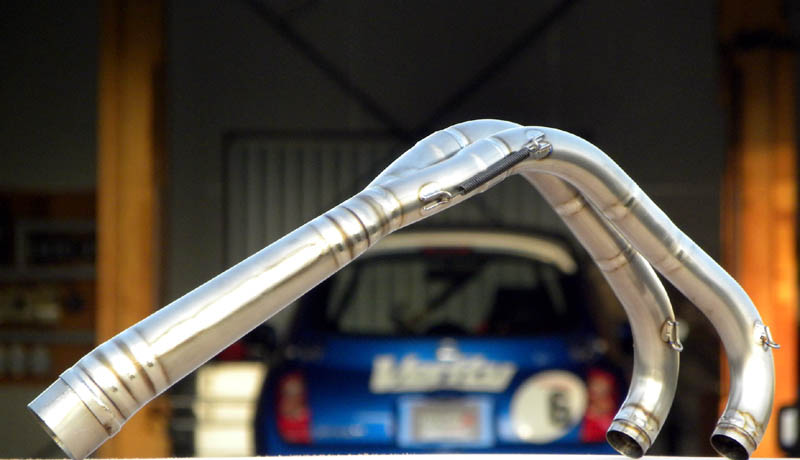
ホームページに紹介した
昔作ったGB500のチタンエキパイを見て、わざわざ広島のお客さんからの依頼
前回は左右2本出しだったが、今回はお客さんの持っている スーパートラップのサイレンサーに合わせて集合
チタンは非常に耐食性が優れているが、グラインダー等で削ると激しく火花を出して燃焼する活性金属だ
活性金属は腐食が激しいのだが、チタンは空気中で一瞬にして酸化皮膜を生成し
その皮膜が内部を保護する為 錆びない
その皮膜生成が熔接作業の障害になる。 チタンの熔接自体は難しくは無い、溶接作業中に いかに酸素を遮断するか
それに尽きる。 いかに不活性ガスでシールドするか、それさえ守れば他の熔接と変わらない
ただ
それが大変なのだ。 その準備も大変だし、作業時間もかかるし、アルゴンガスも大量に使うし・・・

岡山での大雨の中のレース。 総合5位、クラス優勝でした、とメールが届いた。 とりあえずちゃんと走ってる。 一安心・・
|
|
【 VFR750 Intercepter
フルエキゾースト・マフラー 】
(Sep/2011)
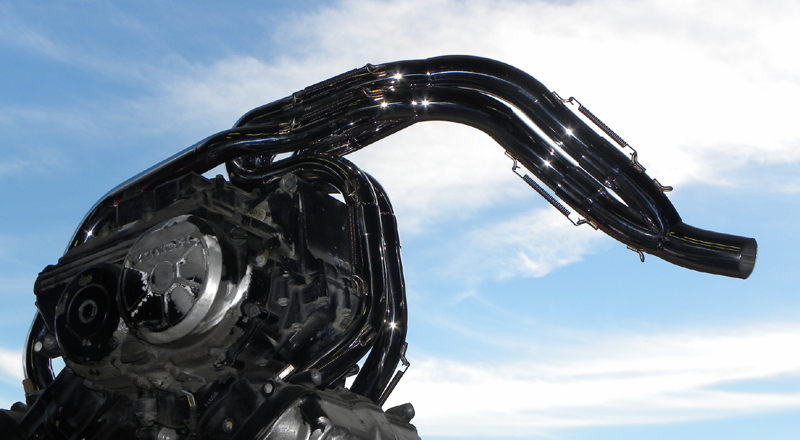
中野のQRという VFR750専門の店の依頼で製作していたフルエキゾーストだが、残念ながら今年
店を閉めてしまったので、製作を引き継いだ
材質はステンレス。 当時のワークス同様のレイアウトで、アルミ外筒のサイレンサーも製作
一番の肝は、クランクケース下で180°Uターンする
リヤバンクのエキパイの曲がり、ワークス部品以上の真円度を保っています
ベンダーでは無理なので、水圧加工で製作しています
|
|
【 エキスパンション
チャンバー 】
(Aug/2011)
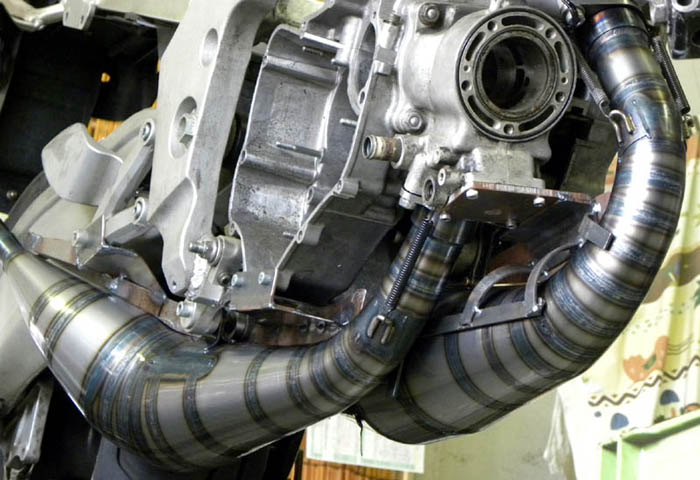
もう生産していない2ストローク車は
もう旧車の部類だが、チャンバー製作を頼まれた。 中身の無いダミーエンジンを冶具にして製作
通常
エキパイ及びダイバージェントコーンまでは、紹介した水圧加工で作るのだが、お客さんの要望で
全て巻いたピースをつないで製作
左右合わせて相当なピース数だ、曲がりのきつい部分や
径の太い部分の曲がりの加工が大変
出来るだけスムーズに仕上げたいが、仕上げに気を取られ過ぎると 肝心の寸法が狂ってしまうので
要注意だ
4ストローク車のエキゾーストは車体部品として認識されているが、2ストローク車のチャンバーはエンジン部品だ
4ストローク車で言えば
カムシャフトに近い程 エンジン性能に影響する
|
|
【 KAWASAKI W1
ペダル改修 】
(Jul/2011)
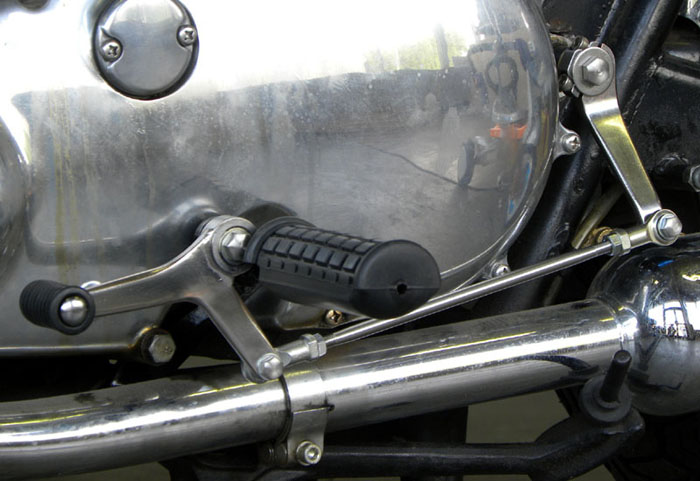
トライアンフ同様 W1も 左ブレーキ 右チェンジペダル で、それを現代風の 左チェンジ
右ブレーキに変更。 トライアンフより作業は楽だが
やはりボルトオンで元に戻せる様にする為、制約が多く
苦労した
カワサキはW3から量産車で逆になっている為、その部品があれば問題ないのだが、もう部品は入手出来ないので 製作を依頼された
やり方は量産車と同様だが、チェンジ側は
かなり長い距離を迂回するので、リンク数も多く複雑になる、当然 作動性が悪化する
その為
1つ1つの部品の精度、リンクのガタ等を、確実に詰めていく必要がある。 チェンジの操作性は量産車を大幅に上回った
|
|
【 撮影用機材
あれこれ 】
(Sep/2011)
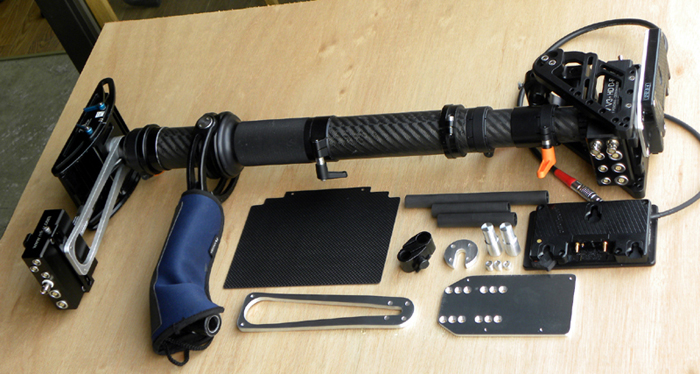
撮影用の機材。 カーボンパイプ等の本体は イギリス製だが、それにバッテリーホルダーや
コネクターボックス等の補記類を
使い易い様に取り付けていく。 フレキシビリティーと軽量化
という相反する問題に悩みながらの製作
【 モニターカバー 】
(May/2011) 【 撮影用人力車
】
(Jun/2011)
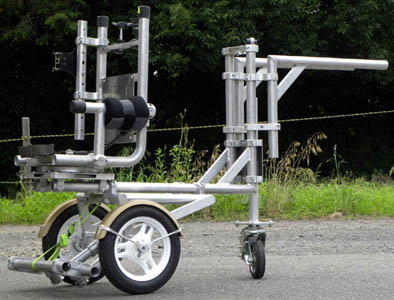
モニター画面を保護するカバーを取り付けた
簡単な仕事だが テレビや映画の撮影用の人力車
普通のカーナビ位に見える
このモニターはプロ用で
回転する椅子に乗ったカメラマンを、2〜3人で引っ張る
強烈な直射日光を浴びても
鮮明に見えるらしい 原始的だが、細い小路での撮影時は、小回りの効く人力車に限る
ステーは
この後、黒アルマイト処理をする トレッドは
600〜900の間で簡単に変更可能、それぞれの部品は
ユニット化されていて
バラバラにして、他の用途にも使用する
タイヤ
ホイール以外全て、構想から 設計 製作までやった
|
|
【 水圧加工
】
(Apr/2011)
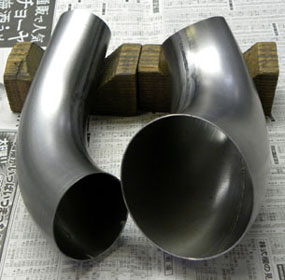
厚さ1mmの鉄板をカット。2枚合わせて熔接し、小さな手押しポンプでキコキコ水圧を掛けると、餅の様に膨らみ
右の写真の様に真円になる
これは 2ストローク車の
エキスパンションチャンバー部品だが、曲がったテーパー管の加工に適した加工方法
プレス等の設備は不要で、手押しポンプさえあれば
誰でも簡単に出来る
ただ
寸法を規制するものは何も無いので、より正確に寸法を出す為には経験が必要になる。 毎回寸法が変わってしまう可能性がある
材料の製造メーカーの違いは勿論、製造ロットの違いでも
差が出る。 今までの膨大な経験値から算出した修正係数を独自に作り
型紙の寸法を決定する
|
|
【 ブレーキペダル改修加工 】
(Mar/2011)
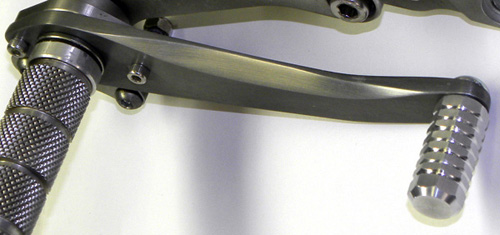
カワサキ ZX12R
に付いていた社外品のステップキットの様だが、ブレーキペダルが何故か
上に湾曲していて、足が当たって
不用意にブレーキが掛かってしまうらしい
ペダルを裏表逆に取り付け、アームが下向きに湾曲する様にし、足が当たらない様に
大きな面取りをして、ペダル部分を削り出し風に作った
機械設備が整っていない事がバレてしまうが、ペダル部分の旋盤加工以外は、全て手仕上げである
その代わり
形状は自由自在だし、作業も早い。 お客さんにも
グラインダーさえあれば、御家庭で自分で出来ますよ。って言ったのだが・・・
|
|
【 NSF100 チタンマフラー改修
】
(Mar/2011)
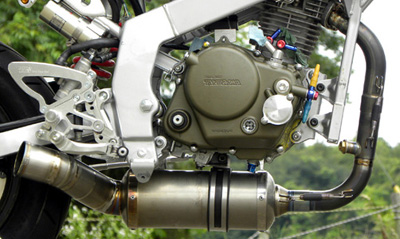
スペシャルフレームに付いていたチタンマフラーを、ノーマルフレームの車体に取り付ける為、曲がり、角度、長さ
の変更をして取り付け改修
簡単な回収作業に思えるが、結局かなりの改修作業になる。 完成品の性能を維持するのは最低眼の要件だから
|
|
【 CBR250
マフラー改修 】
(May/2011)
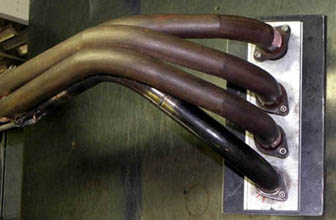
錆び錆びのマフラーだが、お客さんにとっては大切なものらしい? CBR250 Bule Fox
のマフラーだそうだが、エキパイを1本紛失。
ジャンクのエキパイを利用して
作ってくれとの事・・・でも1本だけ違うよ? それでもいいと言うので・・・
車輌がないので
例え簡単な仕事でも冶具を作らなければならない。
フランジ部の間隔はマニュアルの写真から寸法を拡大して算出
|
|
【 ロータスヨーロッパ トレーリングアーム改修
】
(May/2011)
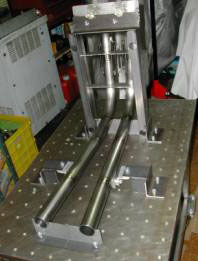
社外品のアームを
イギリスから取り寄せたが、左の写真の様にアライメントが全く合わない為、取り付けプレートを作り直した
単品加工の為、冶具板に簡易冶具を作って作業を行う。 右写真のマフラーも 単品製作の為、同様の方法で
終わったら
簡易冶具は冶具板から外して保管する。 バラバラになるので保管場所を取らない。
冶具板は均等に50mm間隔でネジが切ってある
|